ЕДИНСТВО КАЧЕСТВА И СЕРВИСНОГО ОБСЛУЖИВАНИЯ
Ужесточение требований к качеству выпускаемой продукции и обострение конкурентной борьбы на фармацевтическом рынке стимулирует разработку, создание и постоянное совершенствование упаковочного оборудования, которое удовлетворяет следующим требованиям:
- микробиологическая стерильность продукта;
- отсутствие в нём механических загрязнений и пирогенов;
- экономичное/эффективное производство с низкими эксплуатационными издержками;
- возможность использования при производстве продуктов массового потребления.
Компания BREVETTI ANGELA была основана в 1977 году г-ном Франческо Консоларо, который еще с 60-х годов активно работал в сфере упаковочных материалов для фармацевтических продуктов. Г-н Консоларо является автором успешных исследований в области методов упаковки и разработчиком оборудования для первичной упаковки парентеральных растворов. С тех пор компания BREVETTI ANGELA активно сотрудничает с фармацевтическими компаниями, предлагая решения, ориентированные на удовлетворение пожеланий и потребностей в области первичной упаковки. Результатом этого плодотворного сотрудничества стала разработка последнего поколения машин SYFPAC®, работающих по передовой технологии BFS (BLOW–FILL-SEAL) «Выдув-Наполнение-Запаивание». Одновременно в компании создаётся и другое упаковочное оборудование: машины FLUIPAC®, CYNOPAC®, MECAS®, BAGPAC® и SACKPAC®. Каждый фармацевтический производитель имеет собственные требования к упаковке, в зависимости от характеристик продукта, его взаимодействия с различными видами упаковочного материала, правил государственного регулирования, экономичности того или иного вида упаковки и требований конечного потребителя. Таким образом, задачей компании, работающей в сфере фармацевтической упаковки, становится тщательное изучение рыночных трендов и производство оборудования, максимально удовлетворяющего требованиям рынка.
BREVETTI ANGELA является 100% клиентоориентированной компанией, начиная свою работу с анализа потребностей вашей компании, чтобы предложить максимально эффективное решение в области фармацевтической упаковки.
ПРИНЦИП BFS ТЕХНОЛОГИИ
Производство асептической упаковки требует особой осторожности и специальных условий для избежания попадания в раствор микробиологических и других загрязняющих частиц. Основную угрозу загрязнения парентерального раствора представляют люди, работающие на производстве, поскольку именно они являются источником микрочастиц органического происхождения. Для обеспечения низкого уровня загрязнения при розливе вблизи открытых контейнеров необходимо соблюдать особую осторожность. Технология BFS «Выдув-Наполнение-Запаивание» позволяет производить емкость для раствора, заполнять ее и запечатывать, используя одну лишь машину. Процесс происходит без участия человека, что дает возможность сохранить необходимые асептические условия, предоставляя следующие преимущества:
1) Сама BFS-машина занимает меньше места.
2) Обслуживание оборудования требует меньшего числа техников и операторов.
3) Вполне достаточно, чтобы BFS-установка была размещена в комнате с классом «чистого помещения» D.
4) Сама технология обеспечивает максимум защиты продукта от возможных загрязнений.
5) Технология освобождает производителя от проблем и затрат, связанных с приобретением и хранением пустых емкостей под розлив продукта.
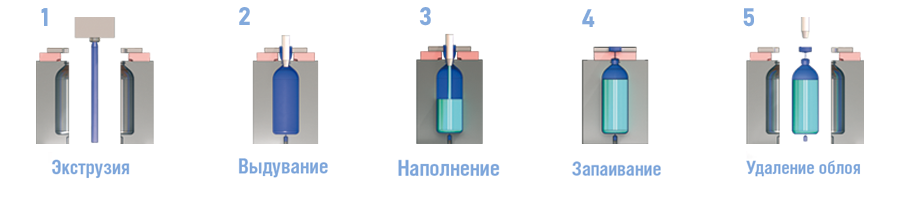
На рисунках 1-5 изображены основные этапы процесса расфасовки инфузионных растворов для парентерального применения в установке SYFPAC®
SYFPAC® является акронимом «System for Filling Parenterals Aseptically into Containers of Plastic materials» (Система для заполнения парентеральных растворов в асептической среде в пластмассовые емкости). Эта система специально разработана для решения проблем, связанных с упаковкой парентеральных жидкостей и препаратов для инъекций. Система SYFPAC® основана на технологическом процессе BFS, при ее разработке использовались инновационные идеи, методы инженерного проектирования, а также передовые материалы и технологии. SYFPAC® разработана для надежной и точной работы на протяжении всего длительного срока службы. Простая и надежная конструкция не требует частого технического обслуживания.
BFS: ТЕХНОЛОГИЯ ВЫДУВАНИЯ, НАПОЛНЕНИЯ И ЗАПАИВАНИЯ
BFS-технология используется в фармацевтической промышленности преимущественно для упаковки растворов. Данная технология применима при упаковке таких растворов, как растворы для инъекций, болеутоляющие средства, антибиотики, глазные капли, растворы, вводимые капельным способом, растворы для диализа, растворы для спринцеваний и растворы для гемодиализа. Рассмотрим её этапы.
Первый этап начинается с экструзии паризона – расплавленного рукава из полимерного материала.Под воздействием вдуваемого воздуха или вакуума (или при комбинации этих двух способов) паризон, принимая форму гнезда пресс-формы, превращается в емкость. Верхняя часть изготовленной емкости открыта и находится в полурасплавленном состоянии до тех пор, пока емкость не будет заполнена и запаяна.
Следующим этапом является наполнение емкости, которое выполняется сверху (верхняя часть пластмассовой емкости все еще находится в полурасплавленном состоянии). Заливочные форсунки входят в верхнюю часть емкости и заполняют ее. Конструкция форсунок упрощает их автоматическую чистку и стерилизацию. Кроме того, форсунки используются для выдувания бутылок и в них предусмотрена отдушина, через которую выходит воздух во время заполнения емкостей. Процесс наполнения может сопровождаться подачей стерильного фильтрованного воздуха, чтобы избежать загрязнения. Воздушный компрессор автоматически регулирует давление подаваемого стерильного воздуха, обеспечивая одинаковую скорость подачи воздуха в разных условиях. Автоматическое устройство управления поддерживает давление потока стерильного воздуха на установленном значении.
На следующем этапе происходит запаивание верхней части сосуда, которая оставалась открытой, пока полимерная масса в этой части находилась в полурасплавленном состоянии. Горлышко сосуда прессуется головками пресс-форм и одновременно с этим охлаждается, происходит формирование верхней части сосуда. В результате получается герметично закрытый сосуд. Конечным этапом является удаление облоя с емкости и его вывод из машины. Вся процедура BFS и удаления облоя занимает от 10 до 18 секунд, в зависимости от типа и размера емкости. Преимуществом технологии BFS является то, что емкость формуется, быстро заполняется и автоматически закупоривается в защищенной среде без участия человека.
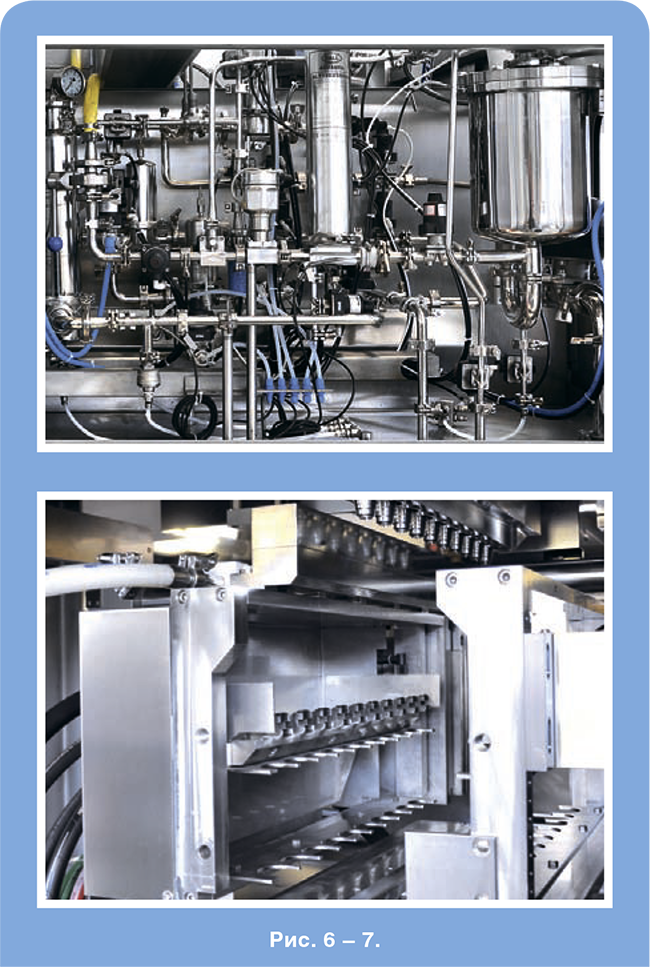
«Для удаления следов предыдущего продукта перед заполнением нового продукта в системе SYFPAC® используется автоматическая процедура CIP (Cleaning In Place Безразборная мойка). Основными параметрами CIP является давление, температура и количество циклов мойки, эти параметры можно отрегулировать после проведения соответствующих практических испытаний. Вдобавок к этому, система SYFPAC® может в автоматическом режиме осуществлять процедуру SIP (Sterilisation In Place Безразборная стерилизация) для стерилизации всего контура наполнения, контура сжатого стерильного воздуха, бака с раствором и фильтров. Кроме того, имеется возможность автоматической сушки фильтров и обеспечения стерильности машины посредством нагнетания в контур стерильного сжатого воздуха. Целостность фильтров можно проверить на месте при помощи дополнительного оборудования (рисунок 6-7).»
ПРОЦЕДУРА УПАКОВКИ В АСЕПТИЧЕСКИХ УСЛОВИЯХ
Поскольку процесс выдува, наполнения и запаивания контейнера происходит на одной машине, защищается нагнетенным стерильным воздухом, а технологические вещества (воздух, раствор) также, в свою очередь, проходят через стерильную фильтрацию, возможность попадания в раствор загрязняющих частиц практически сведена к нулю. Учитывая тот факт, что во время всего цикла открытая емкость взаимодействует с атмосферой «чистой комнаты» менее 1,5 секунды, технология BFS является наилучшим выбором, если вашей главной целью является избежание загрязнений посторонними частицами.
МАШИНЫ BFS ДАЮТ ГИБКОСТЬ В ВЫБОРЕ УПАКОВОЧНЫХ МАТЕРИАЛОВ
Первичная упаковка (емкость) защищает содержимое от попадания загрязнений из окружающей среды: от микроорганизмов и от посторонних частиц. Кроме того, емкость защищает активное вещество и/или эксципиент от диффузии, обеспечивая стабильность продукта, а также защищает содержимое от света и газов, присутствующих в окружающей атмосфере. Помимо этого, необходимо иметь в виду, что раствор соприкасается с имеющимися в пластмассе добавками. Pharmacopoeia has set limits on the …
В фармакопее указаны ограничения на содержание добавок в пластмассе, использующейся в медицинских целях, а также перечень добавок, запрещенных к использованию в пластмассе, из которой изготавливаются емкости для фармацевтических продуктов. Ежедневно многие известные компании производят медицинский полипропилен и полиэтилен, который разрешено использовать для производства емкостей для внутривенных и инъецируемых растворов. Несмотря на то, что емкость, изготовленная при помощи технологии BFS, является стерильной, правила организации производства некоторых стран, а также фармакопея США и стран Европы предписывают обязательную окончательную стерилизацию продуктов, которые можно подвергнуть стерилизации паром. Европейское медицинское агентство по оценке лекарственных препаратов (EMEA) рекомендует производителям использовать упаковочные материалы, которые можно подвергать окончательной стерилизации, соблюдая указания по температуре и длительности стерилизации. Ввиду указанных выше причин, машины BFS являются лучшим решением для фармацевтической отрасли, поскольку их можно использовать для изготовления емкостей из широкого набора материалов (полиэтилена высокой плотности, полиэтилена низкой плотности, полипропилена).
СПЕЦИАЛЬНАЯ ЗАЩИТНАЯ АТМОСФЕРА И ПРОДУВКА ИНЕРТНЫМИ ГАЗАМИ
Чтобы избежать окисления продукта, пространство над жидкостью можно заполнить инертным газом (азотом, углекислым газом).
РАССМОТРИМ ПОПОДРОБНЕЕ, ЧТО ЖЕ ПРЕДСТАВЛЯЕТ ИЗ СЕБЯ BFS-МАШИНА
МАТЕРИАЛЫ, ИЗ КОТОРЫХ ИЗГОТОВЛЕНА МАШИНА
Тщательный подбор материалов, входящих в контакт с фармацевтическими жидкостями, и самосмазывающиеся детали позволяют использовать машину в «чистых комнатах» для асептической упаковки и обеспечивают эффективное использование также в коррозионной среде. Эргономичная конструкция компонентов обеспечивает простой доступ во время техобслуживания и чистки.
ВСТРОЕННЫЙ ГЕНЕРАТОР ВАКУУМА И УСТРОЙСТВО ДЛЯ СНЯТИЯ ОБЛОЯ
Машины оснащены генератором вакуума и автоматическим устройством для снятия облоя, а гидравлическая система оснащена пропорциональными клапанами управления с электронной регулировкой, обеспечивающими более равномерную работу.
«Универсальная конструкция машины SYFPAC® позволяет использовать широкий спектр полимеров без необходимости заменять пресс-формы. В машине SYFPAC® можно использовать следующие полимеры:
• медицинский полиэтилен низкой плотности для экструзии и выдувания LOW DENSITY POLYETHYLENE (LDPE).
• медицинский полиэтилен высокой плотности для экструзии и выдувания HIGH DENSITY POLYETHYLENE (LDPE).
• медицинский полипропилен для экструзии и выдувания POLYPROPYLENE (PP).
Возможность использования пластмасс различных типов упрощает поиск на местном рынке материалов, совместимых с фармацевтическим продуктом, улучшая при этом его стабильность. В экструдер можно установить специальное приспособление, позволяющее добавлять к гранулам определенное количество красителей или специальных добавок перед экструзией, благодаря чему можно изготовлять цветные емкости или емкости, обладающие особыми характеристиками, например, блокирующими проникновение ультрафиолетовых лучей и т.д»
ПАНЕЛЬ И ИНТЕРФЕЙС УПРАВЛЕНИЯ МАШИНОЙ
Система управления осуществляет указанные ниже функции в автоматическом режиме:
— Осуществление SIP, CIP, сушки фильтра и обеспечение стерильности.
— Выполнение предварительных операций, необходимых для проверки целостности фильтра.
Управление, осуществление и мониторинг всего цикла BFS в автоматическом режиме, снятие облоя и выпуск емкостей.Контроль, мониторинг и управление в ручном режиме.Мониторинг и регистрация критических параметров функционирования машины. В случае, если один из параметров выходит за пределы допустимого диапазона, оператору подается звуковой и визуальный сигнал. Регистрация событий во время работы (архив сигналов тревоги).Интерфейс для ручного управления состоит из клавиатуры, панели управления и цветного экрана. Имеются несколько уровней доступа пользователей.
Интерфейс ручного управления позволяет следующее:
- Программирование параметров SIP, CIP, контроля целостности фильтра и другие параметры, такие как температура экструдера и время выполнения различных фаз цикла машины. В случае необходимости, сотрудники эксплуатационной службы при помощи интерфейса могут задать минимальные/максимальные пороги параметров.
- Позволяет отображать параметры, необходимые для работы машины.
- Отображает производственные данные, например, часы работы, расход раствора, расход пластмассы и т.д.
- Отображает критические параметры, например, температуру, давление и т.д. во время SIP, CIP и других важных операций по подготовке машины.
- Позволяет отображать, архивировать и регистрировать аварийные сигналы, как активные, так и возникшие ранее.
- Дает указания по выполнению определенных работ техобслуживания.
- Позволяет отображать и устанавливать значения механических параметров, таких как движение прессформы (закрытие и перемещение) и ее торможение.
ТИПЫ ЕМКОСТЕЙ, КОТОРЫЕ МОЖНО ПРОИЗВОДИТЬ НА BFS-МАШИНЕ
Благодаря универсальному производственному процессу, при помощи машины можно изготовить и наполнить разнообразные типы емкостей различных размеров, используя одно из многочисленных решений. Объем емкости может составлять от 0.2 мл до 13 литров. Можно изготавливать емкости различных форм, как жесткие, так и гибкие, поддающиеся сжатию, сосуды. Как правило, жидкость выпускается через верхнюю часть емкости и для упрощения ее подачи можно изготовить горлышко подходящей формы, в том числе с резьбой для установки соединителей или крышек. Есть возможность изготавливать пресс-формы с несколькими полостями из нержавеющей стали и специальных сплавов бронзы с передовыми охладительными и вакуумными контурами, встроенными в пресс-форму, обеспечивают равномерное производство емкостей (бутылок, ампул, сосудов). На пресс-формы можно наносить градуированную шкалу, указывающую на количество оставшейся жидкости. Кроме того, имеется возможность заказать вставки для рельефной печати номера партии и логотипа компании на поверхности емкостей.
БЛАГОДАРЯ ТЕХНОЛОГИИ BFS, КОНЕЧНЫЙ ПРОДУКТ ОБЛАДАЕТ СЛЕДУЮЩИМИ СВОЙСТВАМИ:
- экономичное и эффективное производство.
- отсутствие посторонних частиц.
- микробиологическая стерильность.
- отсутствие загрязнений.
- содержится в требуемой атмосфере.
ПРЕДНАПОЛНЕННЫЕ ШПРИЦЫ С BFS МАШИНОЙ SYFPAC® SECUREJECT®
На данный момент наблюдается тенденция к повышению спроса на преднаполненные шприцы. Работники здравоохранения используют преднаполненные шприцы, так как признают их наиболее выгодными в силу очевидных преимуществ:
- они позволяют снизить уровень переполнения, что позволяет уменьшить расходы;
- их применение определяет резко положительное отношение больных к использованию данного продукта;
- просты в применении как для медработников, так и для пациентов;
- их применение снижает риск контаминации и ошибки дозирования;
- утилизация преднаполненных шприцев уменьшает возможность повторного использования, а, следовательно, перекрестного инфицирования.
ПОЧЕМУ ПРЕДНАПОЛНЕННЫЕ ШПРИЦЫ НЕЧАСТО ИСПОЛЬЗУЮТ В ОБЛАСТИ ПРИМЕНЕНИЯ ВОССТАНОВЛЕННЫХ ПРОДУКТОВ?
Основные растворители, применяемые для восстановления лиофилизированных (сублимированных) продуктов: NaСl и WFI. В настоящее время большинство этих растворителей пакуются и поставляются в ампулах. Затем, чтобы извлечь растворитель из ампулы и смешать его с лиофилизированным препаратом, находящимся во флаконе, требуется использовать стерильный шприц. Эти действия можно сделать более простыми и безопасными, если растворитель будет упакован в преднаполняемые шприцы. Как бы то ни было, большинство преднаполненных шприцев поставляются в клетях или матрицах от нескольких десятков до нескольких сотен стерильных, готовых к наполнению шприцев. Несмотря на более высокую стоимость, пустые преднаполненные шприцы и соответствующая наполняющая машина все еще наиболее популярный метод.
ПРЕДНАПОЛНЕННЫЕ ШПРИЦЫ С BFS МАШИНОЙ
Глобальная эпидемиологическая ситуация, связанная с пандемией COVID-19, старение населения планеты, а также растущее число производителей дженериков – все это стимулирует к увеличению производств вакцин с одной стороны, и снижению производственных расходов с другой. Можно добиться снижения затрат в несколько раз, если есть возможность производить данные шприцы с помощью BFS технологии, так как:
- это позволяет уменьшить количество этапов производства;
- технология позволяет производить преднаполненные шприцы на площади 50 м² в течение нескольких секунд из полимерных гранул, стоимостью лишь в несколько центов;
- позволяет исключить затраты на вторичную упаковку;
- полимерные шприцы — первичная упаковка. Эти контейнеры не бьются при нормальном обращении и транспортировке;
- полимерные шприцы могут иметь более высокий допуск и сниженную овальность внутреннего диаметра по сравнению со стеклянными шприцами. Это позволяет уменьшить необходимую для нажатия на поршень силу;
- пластиковые шприцы исключают вероятность наличия вольфрамовых следов (вольфрам способен вызвать каталитическое расслоение или некие биологические соединения, белки могут агломерироваться с вольфрамовым остатком);
- пластиковые цилиндры не требуют силиконизации, таким образом, исключаются проблемы, связанные с силиконом.