Автор: Андрей Коробов, Директор по развитию информационных технологий АО «ПРОМИС»
В 2022 году российские компании столкнулись с рядом проблем в сфере маркировки, в том числе с отсутствием технической поддержки от зарубежных производителей оборудования по сериализации и агрегации, риском ухода с рынка поставщиков иностранного программного обеспечения и отсутствием его обновления. Директор по развитию информационных технологий АО «ПРОМИС» Андрей Коробов рассказал о ситуации на рынке оборудования и программного обеспечения для маркировки, а также о перспективах его развития в будущем.
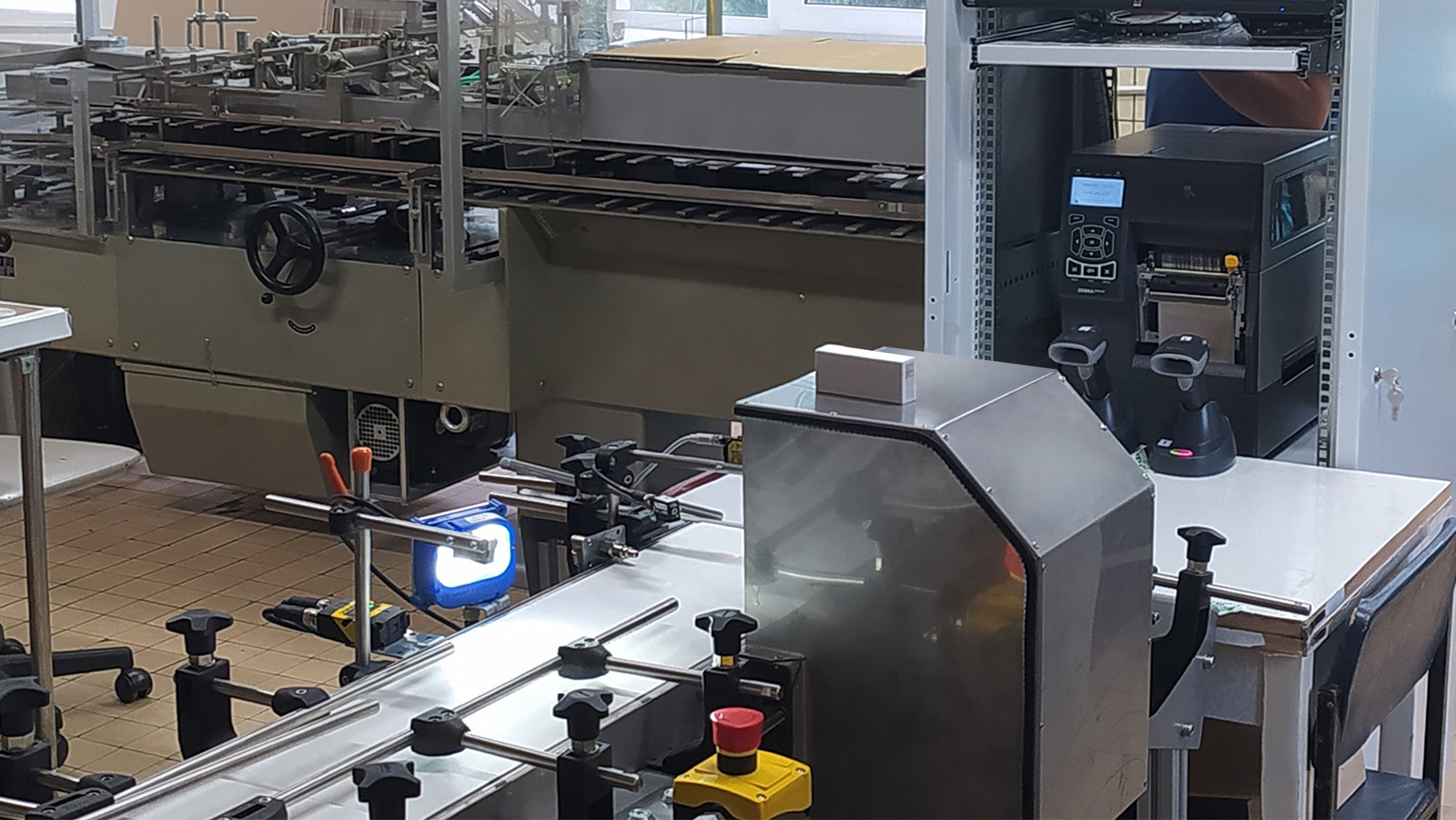
Рис 1. Система поточной сериализации и агрегации.
О МАРКИРОВКЕ ЛЕКАРСТВЕННЫХ ПРЕПАРАТОВ
– На наш взгляд, процесс маркировки лекарственных препаратов состоялся: отработана как методологическая, так и техническая база. На первых этапах было много проблем, касающихся нанесения 2D-кода на упаковку товара, но сейчас все знают, что наносить и как наносить, не допуская ошибок.
Большая работа была проделана Центром развития перспективных технологий (ЦРПТ). Благодаря реестру интеграторов, в который входит и АО «ПРОМИС», фармкомпании знают к кому обращаться для покупки качественного оборудования и ПО. Для маленьких предприятий, которые не могут позволить себе крупный проект, ЦРПТ выпускает отдельные программные решения. В качестве поддержки небольших компаний в «ПРОМИС» был разработан программно-аппаратный комплекс «ПроСалекс SE» для нанесения этикеток с 2D-кодом.
В целом информационная система маркировки работает стабильно настолько, насколько такая глобальная структура может функционировать.
О МАРКИРОВКЕ БИОЛОГИЧЕСКИ АКТИВНЫХ ДОБАВОК
– Нами накоплен опыт в сфере маркировки лекарственных препаратов и, конечно, мы хотим транслировать его на другие товарные группы, первыми из которых станут БАДы. Их маркировка несколько отличается от лекарств: упрощается наносимая информация, как и все бизнес-процессы, которые будут реализовываться.
Используя платформу качественного, стабильного программного обеспечения «ПроСалекс», мы создали специализированный интерфейс для маркировки БАД на базе той же технологии, которую применяли для лекарственных препаратов. Для пользователей это означает высокую стабильность функционирования и минимальное количество действий оператора. Большая часть процессов полностью автоматизирована, в том числе и алгоритм взаимодействия с информационной системой регулятора ФГИС МТ.
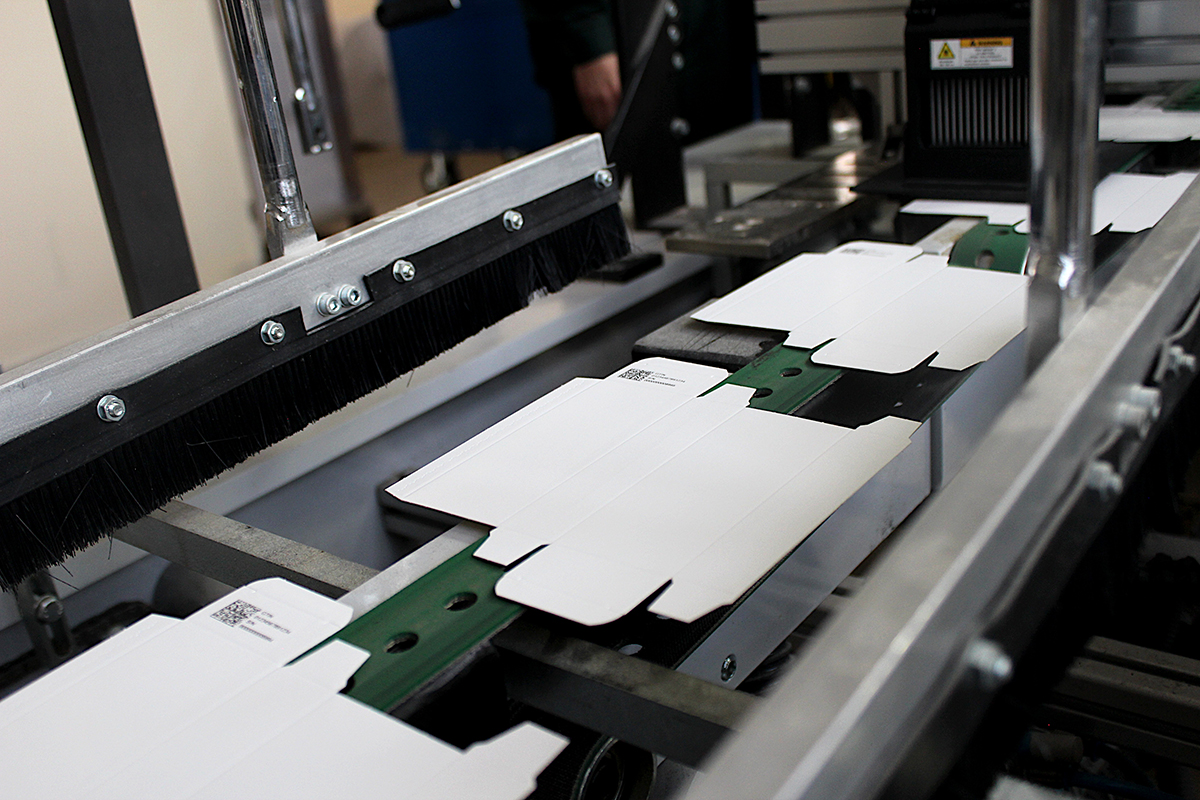
Рис 2. Нанесение 2D-кода в АО «ПРОМИС».
ОБ ИМПОРТОЗАМЕЩЕНИИ
– Изучая потребности наших действующих и потенциальных клиентов, мы поняли, что опыт маркировки лекарств подталкивает нас к созданию несложного и недорогого оборудования, способного заменить импортные образцы, которые в настоящий момент в Россию не поставляются. Например, у нас есть собственное оборудование для ручной маркировки, актуальное для низкопроизводительных линий. Также имеется довольно интересное решение JetPacker, которое работает в сочетании с любыми вариантами нанесения 2D-кода.
JetPacker – это программно-аппаратный комплекс, в том числе система второго уровня, предназначенный для подключения сканирующих верифицирующих устройств. Он позволяет с минимальными затратами повысить производительность процессов сериализации и агрегации.
JetPacker осуществляет функции автоматического сканирования промаркированых упаковок и распределения потоков между двумя операторами-укладчиками. Когда набирается нужное количество упаковок для формирования одного гофрокороба, система автоматически переключает поток пачек с одного сотрудника на другого. В этот момент первый работник перемещает упаковки в гофрокороб и наклеивает транспортную этикетку.
Операторов не нужно долго обучать, они работают в комфортном режиме без лишних трудозатрат. А если им удобно, то их производительность будет расти: с JetPacker фармкомпаниям за небольшие деньги удается достичь скорости, сравнимой с автоматическими линиями. Особенно эффективно это решение в сочетании с пачками с нанесенным 2D-кодом в «ПРОМИС». В этом случае производителю фактически останется только поместить препарат в упаковку, будь то БАД, или лекарство.
Мы конструируем наше оборудование из доступных, понятных компонентов, поэтому нашим заказчикам не приходится выстраивать сложную технологическую цепочку, предполагающую поиск дорогостоящего оборудования, грамотных наладчиков, заключение дорогого сервисного контракта и создание склада запчастей. Основным ноу-хау является ПО для управления этим оборудованием и отлаженный верифицированный бизнес-процесс.
О ЦЕНАХ НА ОБОРУДОВАНИЕ
– Нужно считать не стоимость первоначальной покупки, а затраты на владение. Например, комплект из двух иностранных машин для полуавтоматической сериализации и агрегации стоит порядка 280 тысяч евро. Много это или мало? Сложный вопрос. В рамках производства расчет будет другим – необходимо также учесть стоимость сервисного обслуживания, обучения инженеров, заказа исключительно оригинальных запчастей, гарантию, которая по российскому законодательству должна быть минимум год, сложности обслуживания и использования, а также подбора определенного персонала. По нашим подсчетам, покупка и первый год владения в сумме выходят в 300 тысяч евро. Отдельная статья расходов это лицензии на программное обеспечение, которое у некоторых производителей требуется продлевать ежегодно.
Коммерческая стоимость нашего решения значительно меньше. Она определяется в зависимости от конкретных наборов опций оборудования, но речь изначально идет о сумме 1–1,5 миллиона рублей.
Кроме этого, заказчик получает отлаженный процесс, который может гибко настраиваться под его нужды, и техническую поддержку, которая разговаривает на русском языке и может оперативно решить возникающие проблемы. В «ПРОМИС» есть полноценное сервисное подразделение, где работают инженеры сопровождения и техники, которые объяснят, как пользоваться оборудованием и ПО, и, если нужно, покажут всё наглядно на предприятии заказчика. И, конечно же, скорость реагирования нашей техподдержки на порядок выше, чем у наших зарубежных коллег, хотя у них тоже очень хорошее оборудование и софт.
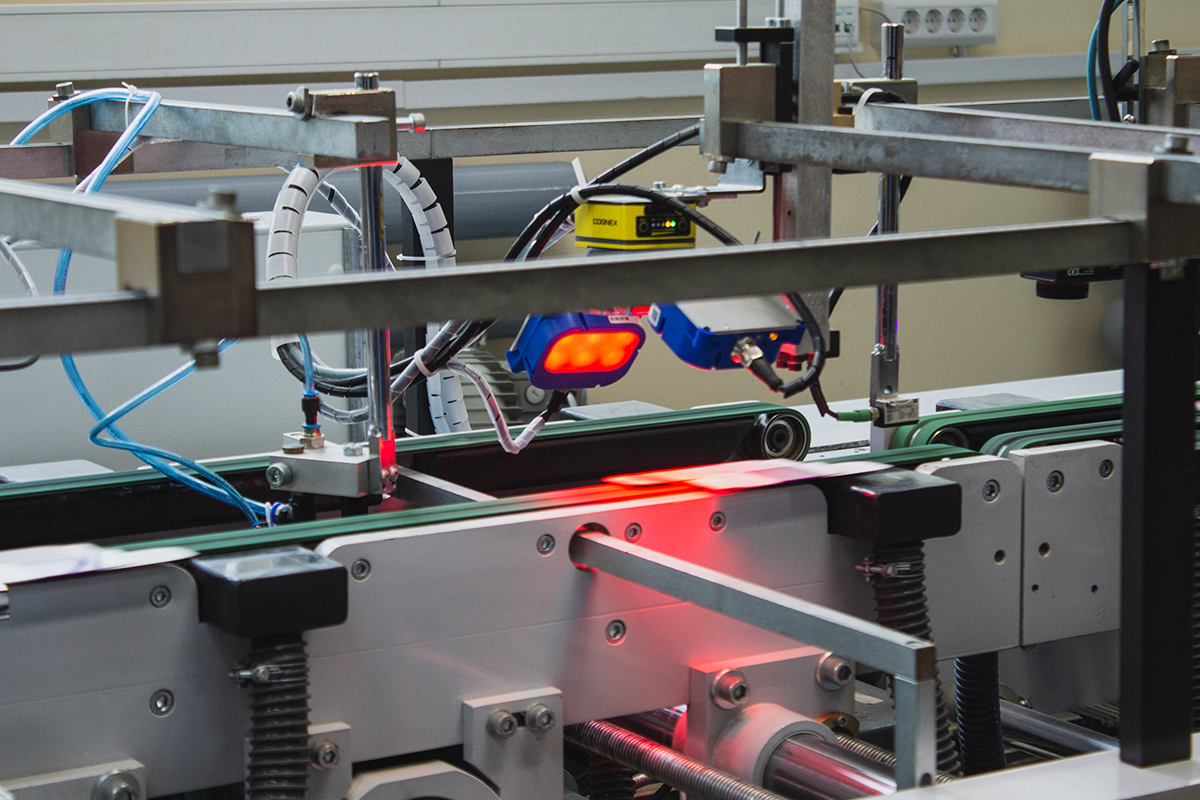
Рис 3. Камера Cognex, установленная на оборудовании.
О ВЛИЯНИИ САНКЦИЙ И РАБОТЕ С КИТАЙСКИМИ ПАРТНЕРАМИ
– Нужно отдать должное тому, что многие поставщики иностранных решений прекрасно понимают, что геополитика – вещь сложная и своеобразная. Компании во всем мире заинтересованы в ведении бизнеса и пытаются наладить новые логистические цепочки. Тем не менее, у некоторых предприятий сохраняются проблемы. Мы, как потребители, столкнулись с отказами в поддержке программных продуктов из-за того, что локальное законодательство поставщика запрещает работать с российскими покупателями.
Производители, работающие на иностранном оборудовании, видят для себя риск непоставки запасных частей для него. Сейчас такие компании задумываются о замене импортного ПО и оборудования.
Кроме того, нужно помнить, что на завод заказчику поставляется не монолитное устройство в черном ящике. Оно состоит из OEM-компонентов, которые разрабатываются разными компаниями. Например, принтеры производит VideoJet или REA JET, камеру машинного зрения – Cognex, сервоприводы – тайваньские компании, большую часть электроники – Китай.
Мало просто купить оборудование, всегда нужно думать о том, как его потом эксплуатировать. Когда началось политическое давление, мы стали искать альтернативы высокотехнологичным компонентам, в первую очередь – камерам машинного зрения. Как оказалось, даже при большом богатстве выбора в Китае далеко не все производители способны предоставить оборудование и набор первичного программного обеспечения с соответствующими сертификатами, подтверждающими, что та или иная камера действительно осуществляет верификацию грейда нанесенного 2D-кода.
Тем не менее, мы нашли и протестировали образцы компонентов, которые предоставляют необходимый функционал. Уже сейчас мы интегрируем подобные устройства в наши проекты.
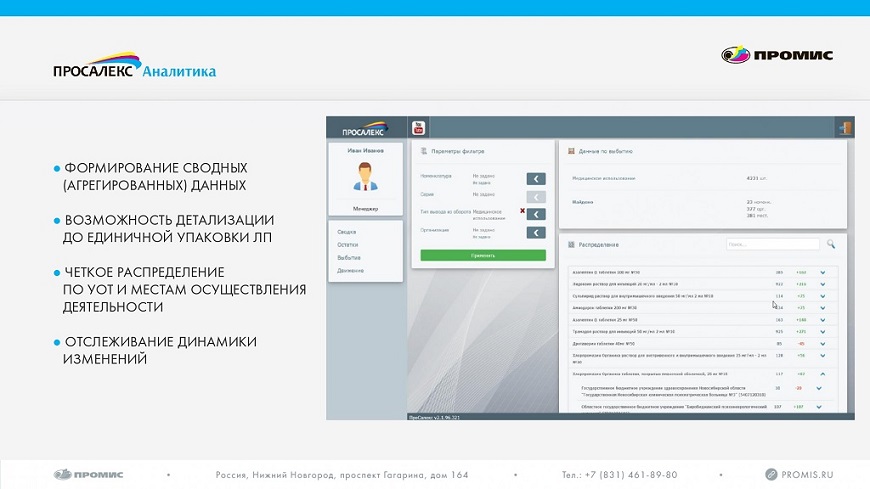
Рис 4. Возможности модуля «ПроСалекс.Аналитика».
СОВЕТ ФАРМПРОИЗВОДИТЕЛЯМ
– Пока непонятно, какими путями можно будет поставить отдельные OEM-компоненты, полагаем, что проблема с заменой комплектующих обязательно проявит себя в течение ближайшего года.
Самостоятельный поиск альтернативы, замена и интеграция компонента – сложный процесс, поэтому мы советуем выяснить у своих поставщиков решений, как они будут ввозить не только общедоступные расходные материалы: ленты, трубки, провода, но и высокотехнологичные компоненты от преимущественно американских и европейских компаний, которые наотрез отказываются поставлять свою продукцию в Россию.
«ПРОМИС» эту работу уже провел, поэтому оборудование, которое мы будем производить, будет выпускаться с уже альтернативными компонентами, либо с возможностью их инсталляции.
ОБ АНАЛИТИКЕ РЫНКА
– Наше ПО «ПроСалекс» всегда было производственной системой, которая позволяет выполнять процессы маркировки. Но мы решили дать нашим заказчикам возможность познакомиться с расширенными сведениями о промаркированной продукции: узнать о движении продукции, о выбытии, об остатках и прочих изменениях статусов в цепочках поставок. Для этого был создан модуль «ПроСалекс.Аналитика».
Он удобен в первую очередь не производственному подразделению, а отделам продаж и маркетинга. Сейчас для того, чтобы узнать о том, как продается лекарственный препарат, нужно заказать аналитику у специалиста, который будет ее собирать около месяца. Наше решение позволяет реализовать полет творческой мысли: заказчики могут зайти в «ПроСалекс.Аналитика», сформировать нужный запрос в любое время и узнать, например, о нахождении товара у конкретного дистрибьютора, или о выбытии лекарственных препаратов в конкретной точке логистической цепочки. Возможности ограничены только теми данными, которые приходят из ФГИС МДЛП.
В будущем мы планируем сделать модуль «ПроСалекс.Аналитика» в виде отдельного проекта, к которому имели бы доступ не только пользователи ПО «ПроСалекс». В его состав будет входить понятное и доступное приложение для анализа данных о перемещении препаратов и отслеживании изменений их статусов в цепочке движения.
АО «ПРОМИС»
Телефон:+7 (831) 461-89-80+7 (831) 461-89-81+7 (831) 461-89-82
E-mail: marketing@promis.ru
Web: https://promis.ru